Today, the world of industrial processes is undergoing a profound transformation. Technologies like the Industrial Internet of Things (IIoT) and Artificial Intelligence (AI) are creating intelligent and efficient systems. Among these, pumping systems are transforming from simple machines to smart devices, leveraging real-time analytics and predictive maintenance. This transformation enhances their efficiency and performance. As pump manufacturers and operators embrace these smart pumping systems, the industry is poised to transition from a product-based model to a service-based one.
The Evolution of Smart Pumps
Industry 4.0, which integrates advanced automation, AI, and big data analytics to develop intelligent industrial processes, is directly responsible for the evolution of IIoT-enabled pump systems. These pump systems have now transformed from reactive maintenance to predicting issues before they arise.
This change is driven by IIoT-connected sensors that continuously monitor key performance metrics like flow, pressure, vibration, temperature, and energy consumption. With the help of AI-ML equipped software evaluate this real-time data that allows stakeholders to find any inefficiencies that may be lying around or foresee mechanical issues as well as improve performance without requiring human intervention. The final result is a fundamental shift in how pump systems operate, leading to increase output, reduces downtime, and increases cost efficiency.
Predictive Maintenance: A Game Changer
One of the key benefits of smart pumping systems is to easily shift from unscheduled to predictive maintenance. Pumps typically undergo maintenance at predetermined intervals, a practice that can sometimes result in unexpected issues. Nevertheless, this challenge can be addressed by adopting predictive maintenance techniques, which detect early indicators of possible malfunctions. By utilizing this method, organizations can prevent expensive downtimes. Also, in settings where pump failures can create significant disruptions, this predictive technique has emerged as a modern breakthrough.
Contribution to Sustainability
As industries strive to reduce energy consumption and environmental impact, AI-ML driven pumping systems play a key role in sustainable industrial operations. In the past, pumps worked at a fixed pace, creating difficulties during low demand period. On the other hand, smart pumps adjust pace in real time, reducing both energy waste and expenses.
Additionally, digital twin technology has emerged as a novel solution for both pump producers and consumers. It help operators to simulate real-world scenarios and predict results. As a result, they can make changes in risk-free environment before applying them on broad scale. By reducing resources and energy waste, these novel solutions effectively contribute to sustainability without limiting industry’s productivity.
Reshaping Industrial Operations
In Industries where fluid mobility is critical, the transition to IIoT and AI- ML powered pumping systems is redefining operational efficiency. These pumps are supported with edge computing, intelligent sensor networks, and AI-powered analytics. This enables them to self-regulate, detect inefficiencies, and optimize performance in real time.
Overall, the integration of IIoT and AI -ML into pump systems has changed various sectors. As the demand for AI-ML backed Pumping Station continue to rise, companies will leverage innovations to create long-term efficiency improvements. In other words, the era of self-regulating pumps has arrived, indicating a big stride towards a more intelligent and sustainable industrial future.
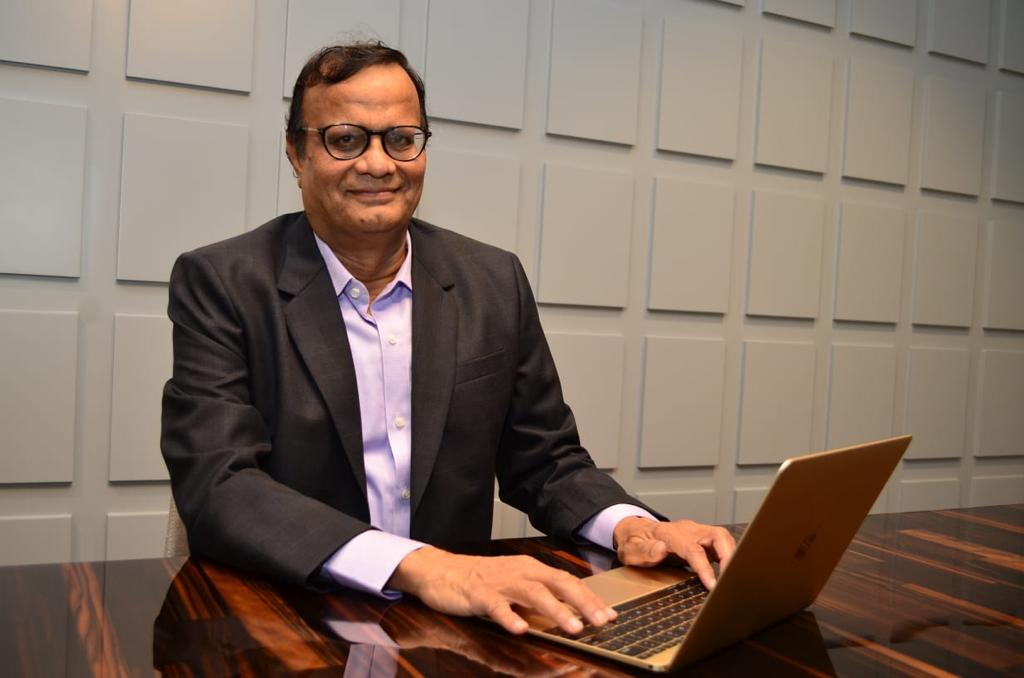
To be attributed to Anil Sethi, Founder & Chairman, Pump Academy Private Limited (iPUMPNET)