When it comes to powering the future of battery electric vehicles (BEVs), the performance of critical components is paramount. Littelfuse’s 1300V A5A Trench Discrete IGBTs are designed with the needs of modern 800V BEV systems in mind, offering a range of benefits that help improve efficiency and reliability in key applications.
These IGBTs offer an optimized collector-emitter saturation voltage (VCE(sat)), enhanced short-circuit robustness, and a broadened current range. They are ideal for use in applications such as PTC heaters, discharge circuits, and pre-charge systems, where the emphasis is on managing high surge currents and minimizing on-state voltage drop, rather than focusing on high switching frequencies.
Background
The automotive industry is increasingly prioritizing sustainability, with battery electric vehicles (BEVs) leading the charge due to their high efficiency and zero tailpipe emissions. In 2023, global sales of BEVs and plug-in hybrid electric vehicles (PHEVs) reached 13.6 million, marking a 31% increase from 2022. This growth is expected to continue accelerating in the coming years.
However, challenges remain. High costs, long charging times, and limited driving ranges still pose barriers to widespread adoption. To tackle these issues, manufacturers are turning to 800 V BEV systems. This advanced voltage architecture facilitates faster charging, significantly reducing both charging times and associated costs.
Silicon is not dead!
Since the early days of electric vehicle (EV) adoption, silicon carbide (SiC) and other wide bandgap (WBG) technologies have been recognized as promising options for various BEV subsystems. WBG materials, with their higher bandgap and significantly greater breakdown voltage compared to silicon, enable higher current densities, faster switching frequencies, and lower overall losses. These advantages allow system designers to achieve better efficiency, smaller system sizes, and reduced weight, especially in applications where high switching frequencies are feasible. As a result, SiC has become the dominant choice for traction inverters, though there are still some exceptions.
However, the maturity of silicon manufacturing processes, the wide availability of options, lower costs, simpler gate drive methods, and the proven robustness of silicon devices mean that silicon power MOSFETs and IGBTs remain strong contenders against WBG technologies. Ultimately, it’s up to skilled designers to choose the most suitable device, and it’s our role as suppliers to provide a comprehensive range of solutions to meet diverse needs.
In applications where low switching frequencies are sufficient, conduction losses and the simplicity of thermal management become key considerations. While WBG devices offer high power density, they can present thermal management challenges. On the other hand, the larger die size of silicon IGBTs and MOSFETs can make thermal management easier in these situations. Many EV subsystems, for instance, don’t require the high switching capabilities that WBG technologies provide, making silicon-based devices a viable choice in those applications.
Applications:
Figure 1: of a generic battery distribution unit (BDU) in an EV

PTC heaters in the thermal management subsystem, pre-charge circuit, and discharge circuit do not necessarily require higher switching frequencies. Instead, these require low conduction losses, high surge current capability, and rugged semiconductors for high reliability.
Thermal Management of BEV
Unlike traditional internal combustion engine (ICE) vehicles, which generate a lot of wasted energy as heat, electric vehicles are far more efficient. However, as a result of that efficiency they do not produce sufficient waste heat to heat the vehicle cabin.[1][2]
In Electric Vehicles (EV) there are two important requirements related with thermal management:
- EV battery conditioning
- Cabin heating in cold ambient conditions
In cold temperatures, PTC heaters and heat pumps are used to regulate the battery temperature for optimal performance, with the heat also providing warmth for the cabin.
Figure 2: Typical circuit configuration for PTC heaters.
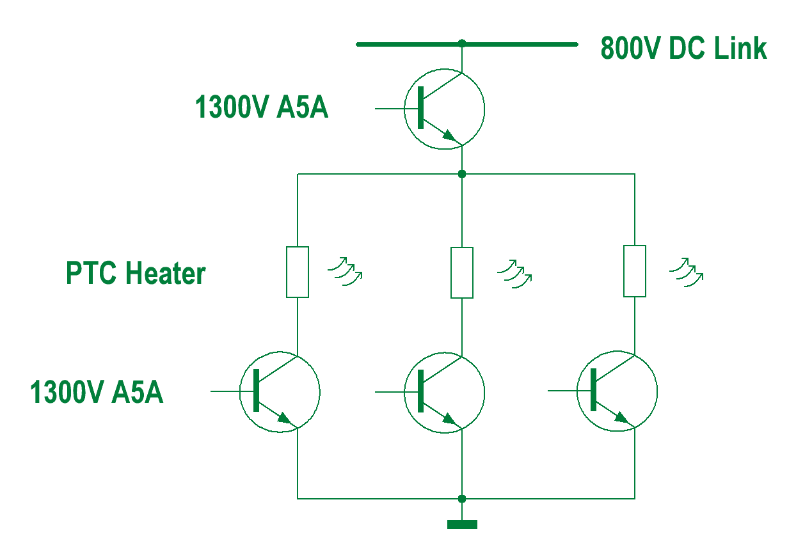
The switching frequency of IGBTs in this application ranges from tens to hundreds of hertz. Low on-state voltage drop, ruggedness (short circuit capability), and good thermal performance of the semiconductor are critical factors for this application.
Discharge Circuit
dc-link capacitor discharge requirements in 800V BEV systems
Critical safety protocols in high-voltage battery electric vehicles require the discharge of DC-Link capacitors in two specific operational scenarios:
- Normal operation shutdown
- Emergency situations like post-collision or critical fault detection
These discharge mechanisms are essential safety features that help reduce the risk of electrical shock to both vehicle occupants and service personnel, while also preventing potential fire hazards. The application is typically classified at Automotive Safety Integrity Level B (ASIL-B), based on the manufacturer’s risk assessment protocols.
In 800V BEV architectures, nominal battery voltage falls within voltage class B (60 V 1500 V) and per ISO 6469-4 [1]safety regulations, the system must ensure rapid voltage reduction in emergency scenarios. Specifically, the bus voltage must be reduced to and maintained below 60 V dc within a 5-second window following vehicle stoppage post-collision.
Figure 3: Typical discharge circuit.
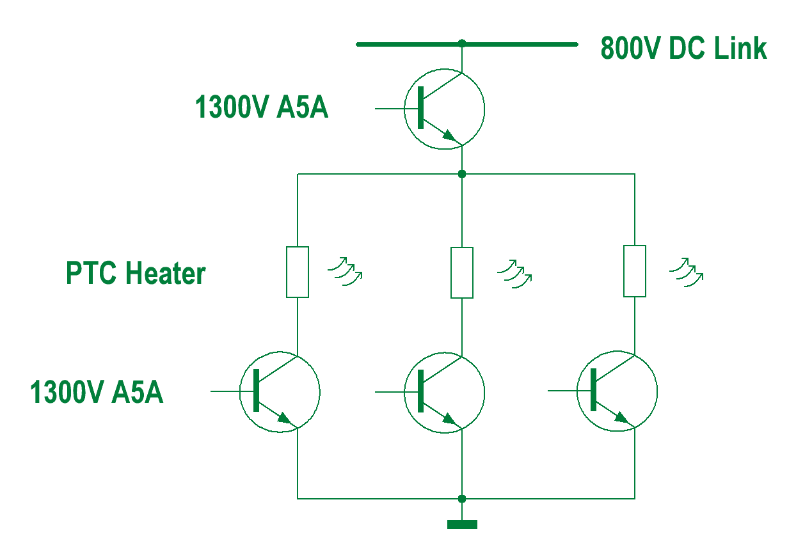
The DC link capacitor can be discharged through an IGBT. When required the IGBT is turned on and all the energy in the capacitor can be discharged via an Rdis resistor in series with the IGBT. Rugged IGBTs with a high surge current capability are of importance for this application.
Pre-Charge Circuit
Pre-charge circuits are widely used in electric vehicles (EVs), including in battery management systems and onboard chargers, as well as in industrial applications such as power supplies and power distribution units. In EVs, the controllers manage the high-capacity electrical components and ensure smooth, efficient motor operation by regulating power flow to the motor. High-voltage positive and negative contactors in pre-charging circuits safely connect and disconnect the power supply to capacitors, preventing excessive inrush currents during startup. They ensure controlled charging and maintain system safety by isolating components when necessary. Without a pre-charge circuit, welding can occur within the contactor during closure, leading to brief arcing and potential damage.
Figure 4: A pre-charge circuit topology
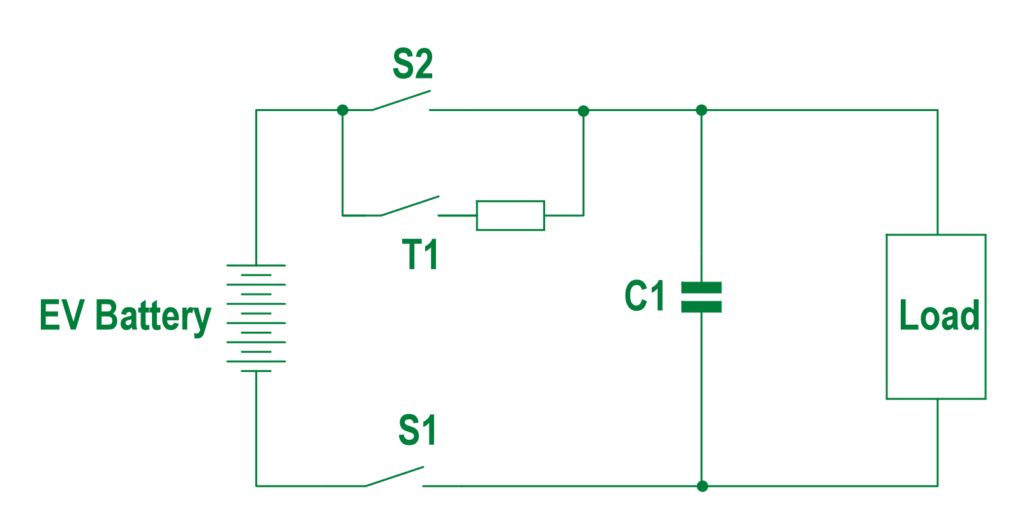
Figure 4 reveals there are two high current, high voltage contactors, S1 and S2, along with a separate pre-charge switch T1, and a DC link capacitor, C1, connected in parallel with a load, such as a traction inverter. Initially, both high-current contactors, S1 and S2, are open, isolating the HV battery from the load at both terminals. Pre-charging begins by closing switch T1 (1300 V A5A IGBT) along with the HV negative contactor S1, allowing the DC link capacitor to charge to a voltage equal to that of the battery. After the pre-charging process, switch T1 opens, and the HV positive contactor S2 closes. As the DC link capacitor was charged before closing the HV positive and negative contactors, there is no significant inrush current. 1300 V A5A IGBTs boast high surge current capability which makes them suitable for this application.
Figure 5: BDU demonstration board by Littelfuse incorporating a 1300 V A5A IGBT.
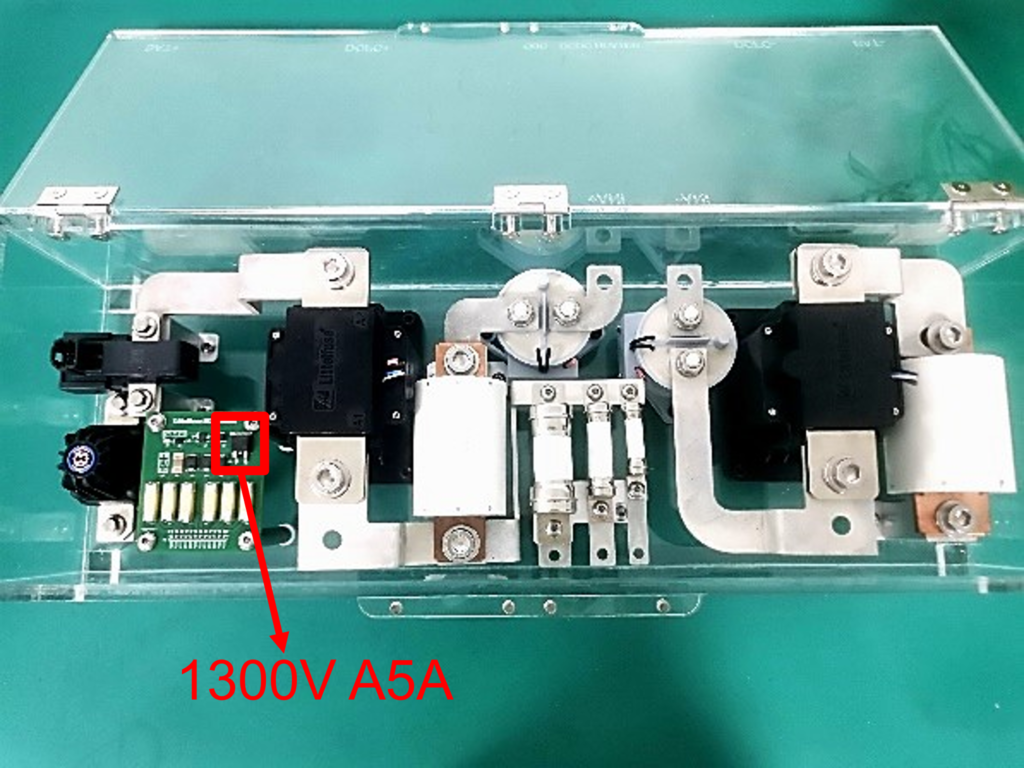
Littelfuse offering- 1300 V A5A Trench IGBTs:
To meet the evolving demands of 800V BEVs, Littelfuse has introduced1300V Trench Discrete IGBTs, see Figure 6. These devices are engineered for applications that emphasize reduced conduction losses (Pcond), good thermal behavior, and ruggedness. The A-Class IGBTs in this series feature an optimized low collector-emitter saturation voltage (VCE(sat)), which enhances their performance in low-frequency switching. These IGBTs exhibit short circuit robustness up to 10 µsec. This is particularly beneficial for critical BEV systems such as PTC heaters which are essential for cabin heating and battery conditioning, these IGBTs are applicable in pre-charge and discharge circuits.
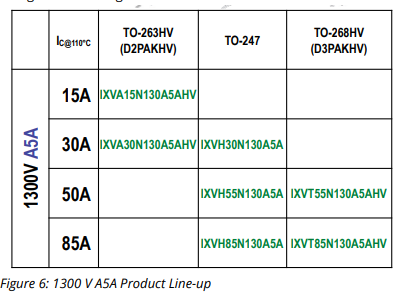
The series includes Single IGBTs in 15 A, 30 A, 55 A, and 85 A collector current at case temperature of 110 °C. The package options are SMD TO-263HV, TO-268HV, and through-hole TO-247. The SMD packages, being HV versions, offer enhanced creepage and clearance compared to the conventional three-pin TO-263 and TO-268 packages.
Engineering samples are available on request contact us at https://www.littelfuse.com/contactus.aspx. Mass production will be in 2025.
Features and Benefits:
Higher Breakdown Voltage BVCES: The 1300 V breakdown voltage is tailored for 800 V BEV architectures, suitable for both passenger vehicles and heavy-duty trucks. This 1300 V rating provides a buffer for the DC link voltage, which fluctuates according to the battery’s state of charge, particularly where a 1200 V rating may pose challenges.
Wider range of currents IC: Collector currents ranging from 15 A to 85 A at 110°C meet the requirements of both passenger and heavy-duty vehicles across various applications.
Minimized Conduction Energy Losses Econd: This series features one of the lowest VCE(sat) values available in 1300 V IGBTs, effectively minimizing conduction losses. This characteristic not only enhances efficiency but also alleviates thermal design challenges.
Short Circuit Capability tSC: The 1300 V IGBTs are engineered to handle short circuit conditions for up to 10 microseconds, making them suitable for automotive applications that require robust performance and enhanced reliability.
Packages: Surface mount discrete packages include TO-263HV, TO-268HV, and the through-hole TO-247. The high voltage (HV) versions of these SMD packages improve creepage and clearance distances compared to standard 3-pin variants.
Summary
As the automotive industry moves toward higher voltage architectures in electric vehicles, silicon IGBTs continue to play a vital role in applications that require lower switching frequencies and minimal conduction losses.
The Littelfuse 1300 V A-Class Trench IGBT family meets the needs of 800 V BEV subsystems, specifically in PTC heaters, discharge circuits, and pre-charge applications. The IGBTs are available with low VCE(sat), short circuit capability, and a wide current range. The availability of both SMD and through-hole packages, with improved creepage and clearance, provides greater design flexibility.