In today’s dynamic world, it’s important to adapt to the latest technologies to sustain the growing competition across the global marketplace. Organizations today must adopt a system that provides continual improvement and meets the customer and regulators’ demands. AS9100-based Quality Management System (QMS) comes as a viable solution that supports compliance with industry standards, operational efficiency, customer satisfaction and overall growth, feels Hariharan Venkitasubramanian
Improved Company Image
Embracing an internationally recognized standard such as AS9100 demonstrates a company’s commitment towards quality management. It’s clear by looking at a few real-time examples that organizations that prioritize and implement high-level quality assurance systems gain more credibility from customers and regulators. Adopting AS9100-based QMS fosters an organization’s marketability, improves its brand image, and opens doors to new opportunities not only limited to just the aerospace sector but also in other sectors as well.
Higher Customer Satisfaction
A key feature of the AS9100 standard is the emphasis on understanding the needs and expectations of the Customers, which varies time to time. By aligning an organization’s processes with AS9100, meeting these expectations can be ensured consistently resulting in increased customer satisfaction and enhanced long-term relationship.
Better Decision Making
AS9100-based QMS focuses more on decision-making with a data-driven approach to empower the top management to be informed about their choices based on substantial evidence. Once the QMS gathers all data and resources in terms of Objectives, Quality, Cost and Delivery and are reviewed periodically, the decision-makers will get a clear view of the critical areas where attention is required. This will facilitate an organization to align better with their goals and business strategies.
Systematic Approach
AS9100 standard incorporates the PDCA (Plan-Do-Check-Act) methodology, a structured approach to quality management. To maintain a high level of quality throughout the product or service life cycle, these methods encourage continuous process definition, implementation, monitoring and improvement. This approach also gives periodic reviews and objective setting in order to streamline the organization’s efforts towards critical areas, ensuring that its processes and outputs are consistently aligned with the requirements.
Increased Efficiency
A salient feature of AS9100 is its process-based approach. It encourages organizations to gain a deeper understanding of how processes interact throughout the product realization cycle. This kind of approach helps in identifying and eliminating inefficiencies within these processes, which results in organizations focusing more on enhancing overall performance.
Engaging Employees
AS9100 harnesses employee engagement by defining the roles and responsibilities of employees and aligning them with the organization’s objectives. This helps in mapping employees at all levels, implementing initiatives to improve their effectiveness, boost their capacity and push them towards achieving their goals and act as a catalyst for the betterment of the organization.
Better Supplier Relationships
It is imperative to build mutually beneficial relationships with the suppliers and work closely with them to ensure that both parties are aligned with the defined goals. Collaborating with the AS9100 standard strengthens the overall supply chain, responsiveness to each other’s requirements. This leads to more reliable delivery of products and services.
Habitual Improvement
Relentless optimization is the core feature of AS9100, making it a systematic and habitual part of an organization’s culture. This framework gives organizations a collective knowledge of their workforce and encourages them to identify areas for process optimization, speed improvement and cost reduction. With this, an organization can continually refine its processes to remain competitive and sustainable.
Last Word
In a nutshell, the overarching idea is to adopt the AS9100-based Quality Management System (QMS) for an organization’s processes in order to strategically improve overall efficiency and customer satisfaction. Embedding this management system into an organization’s DNA can help in improving all aspects including employee engagement, supplier relationships, decision- making strategy and much more. For companies to set benchmarks in their industry and achieve sustained success, AS9100 is an inevitable tool capable of driving growth, operational efficiency and long-term sustainable competitiveness.
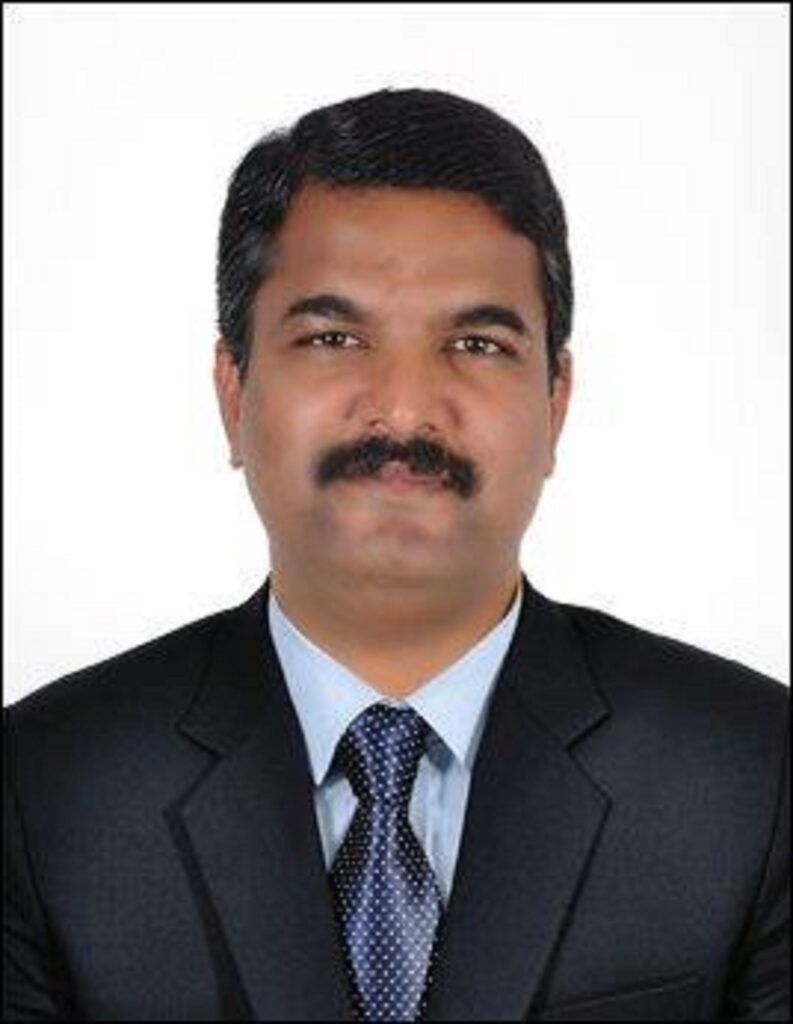
The author is Hariharan Venkitasubramonion -Sr.Manager QA, at Data Patterns India Limited