EV battery structure has significantly developed since the early mass produced vehicles. These developments have been in all components, from cell format and size to thermal management, interconnects, and the enclosure itself. Metals like steel and aluminum have generally dominated battery enclosures, but the lid specifically has provided opportunities for alternatives. This article will discuss the pros, cons, innovations, and adoption of composite covers for EV batteries. IDTechEx report “Materials for Electric Vehicle Battery Cells and Packs 2025-2035: Technologies, Markets, Forecasts”, predicts that the market value for reinforced polymers in EV battery enclosures will grow 10-fold between 2024 and 2035.
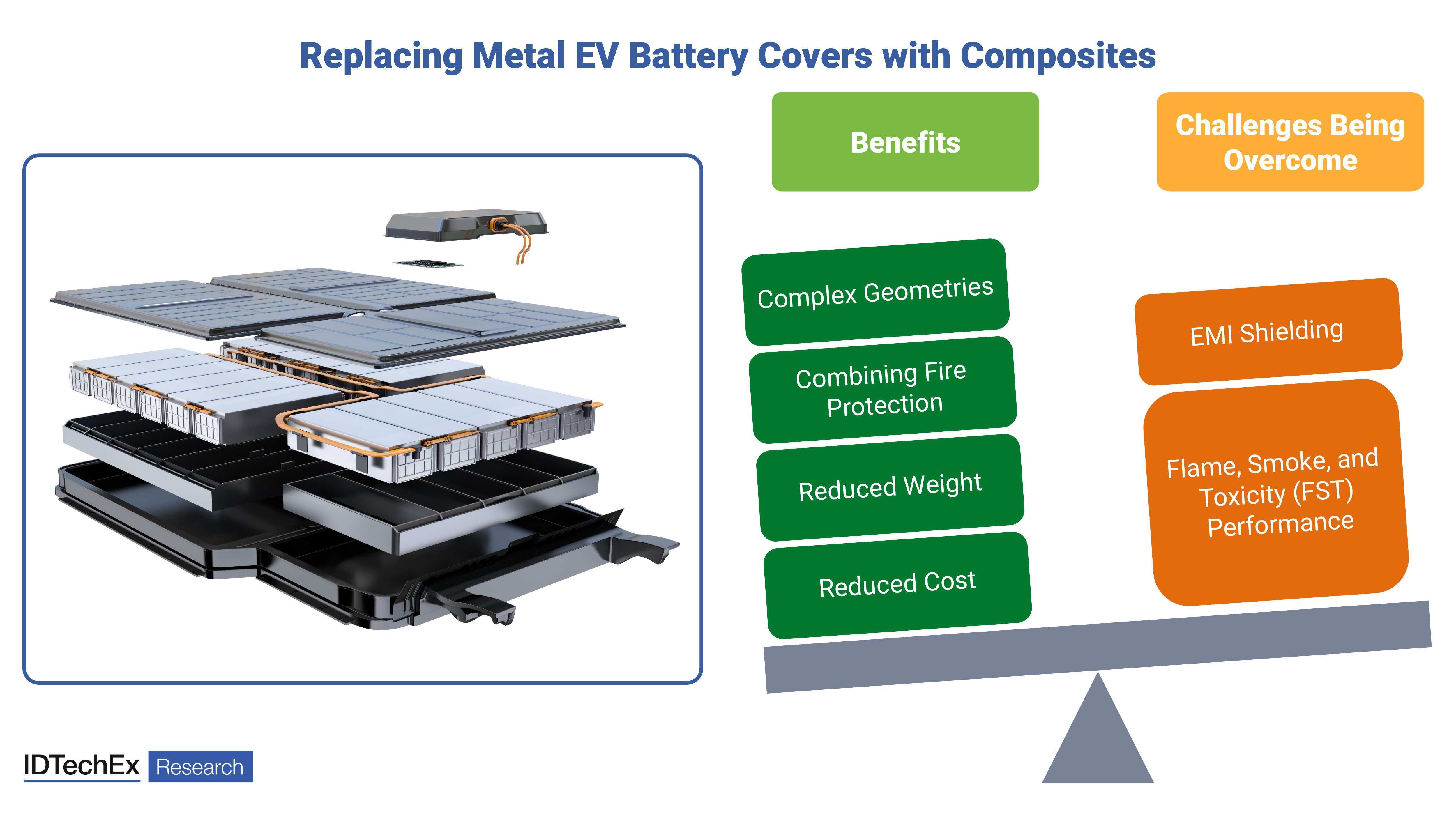
The challenges with composite battery covers are being overcome and their benefits realized. Source: IDTechEx
The benefits of a composite cover
Composite covers can provide various benefits. The first is a reduced weight compared to metals. SMCs (sheet molding compounds) typically have a density in the range of 1.5-2g/cm3. Compare this to aluminum at 2.7g/cm3 or steel at around 7.8g/cm3. The lid does not typically need to be a structural component; therefore, the glass or carbon fiber fill content can be tuned to meet density and fire safety requirements. With less structural performance, the lid can be kept relatively thin, and weight savings could be in the range of 30% for the lid itself.
Composites can also be molded to unique geometries with thicknesses varying across the part for where it is needed. This can result in more flexibility in the design of the top cover.
The challenges with composite covers
One of the major challenges with composite covers is their FST (flame, smoke, and toxicity) performance in the event of a thermal runaway or a fire. Additionally, while metals are naturally EMI shielding, composites are typically not, so a thin metal foil is typically added. This increases costs and adds another manufacturing step. The adhesive alone for the added EMI shielding layer can be several dollars per vehicle.
Innovations in composite covers
With the potentially large market for battery covers, many materials suppliers are innovating to overcome these issues. For example, some players integrate EMI shielding into the initial material formulations, or at the molding stage for the final part.
Many players are also now testing their composite materials to the newer UL2596 tests for torch and grit or BETR tests, as well as a host of other thermal runaway-related tests that are much more strenuous than UL94 tests that most polymers are tested to. With some of these newer formulations, the toxicity concerns in processing and under high temperatures are greatly reduced or eliminated.
A common approach to fire protection in an EV battery is to use a mica shield below the metal cover. With some of the thermal runaway-resistant composites, the cover and shield could be replaced with a single cover that provides fire protection and EMI shielding. Given that it replaces multiple materials, it can reduce the cost of materials and manufacturing.
Examples in the EV industry
Early examples of EVs with composite battery covers include the Chevrolet Volt, the Fiat 500e, and the VW e-Golf. However, more recent vehicles taking this approach too, including the Ford Mustang Mach-E and certain models from BYD, including the Atto 3. It is not yet the most common approach, and it somewhat depends on the design philosophy. Some are now mounting the vehicle seats directly to the battery cover, which tends to be more common with an aluminum cover.
Key examples of companies producing these composite covers include major materials suppliers like Envalior, SABIC, Mitsubishi Chemical, Solvay, and a range of other major players. Some smaller players are getting involved in this space, with key differentiators like combining fire protection and EMI shielding, to try and promote their products, including companies like UK-based FTI Group and TRB Lightweight Structures.
Summary and outlook
With the ever-increasing focus on cost and weight reduction, and fire safety, new composite formulations provide alternatives for battery designers over existing metal solutions combined with fire protective sheets. IDTechEx’s report “Materials for Electric Vehicle Battery Cells and Packs 2025-2035: Technologies, Markets, Forecasts”, predicts that the market value for reinforced polymers in EV battery enclosures will grow 10-fold between 2024 and 2035.