The industrial landscape is undergoing a tremendous transformation driven by cutting-edge technology.The concept of a ‘digital twin’ plays a pivotal role in this evolution, providing operators with greater visibility and control over complex systems. . Notably, the use of digital twins in pumping systems represents a significant advancement in the industry.
Digital twins can be defined as virtual representations of assets or processes associated with assets; in the case of pumping systems, such work often requires designing and developing digital copies of physical pumps as part of a pumping system’s maintenance program. Digital twins of pumps incorporate not only their geometry but also material properties, operational features, and environmental conditions into a comprehensive model. Digital twins of pumps not only represent their physical form; they can also display material properties, functional characteristics, operational context, and environmental conditions. These virtual models allow 360-degree simulations of operating conditions enabling engineers and operators can run performance evaluations and failure scenario analyses. Such foresight is crucial for optimizing maintenance and operational tasks associated with the pump.
Predictive maintenance can be enhanced by digital twins. Incorporating real-time data from intelligent sensors installed on tangible pumps, digital twins study performance patterns to identify any anomalies that point towards failures in the making, and take timely action to mitigate the costs of repairs and loss of productivity. Vibration, temperature and fluid dynamics data are analysed to predict when bearings may sustain damage or when impeller blade erosion will increase, leading to proactive measures being taken before failure occurring. Going beyond simple monitoring, digital twins enable a shift from reactive to proactive maintenance strategies. This process is vital for smart pump monitoring and pumping station operational efficiency, ultimately contributing to reducing life cycle cost and excessive energy consumption.
Additionally, digital twins aid in the improvement of processes related to design and optimisation. Engineers can utilise virtual models during the design phase for testing various operational parameters and evaluating pump performance – helping identify any shortcomings or inefficiencies well before the construction phase begins. Setting up several simulations altering elements such as viscosity of fluid or flow rate adjustments helps ensure a design that is reliable and cost-efficient. This virtual testing eventually lessens the need for costly physical prototypes and accelerates the design cycle. This contributes to AI-driven pump optimisation and the development of energy-efficient water pumping systems, ultimately promoting sustainable pumping technology.
Digital twins also offer another vital benefit – real-time monitoring. Through an integrated pump performance improvement dashboard, an operator can observe and visually inspect a pump’s performance at any moment, providing informed decisions regarding how to best conserve energy and lower costs. It may also help them determine optimal velocities and flow rates for specific applications so as to lessen excess consumption. Apart from this, it may also train operators and help them gain the skills required for error-free execution of tasks. This loop formed by real-time monitoring empowers operators to make more informed decisions that enhance efficiency and reduce operational costs, contributing to pumping system automation.
This technology is not only extremely useful for real-time monitoring but also essential in monitoring and diagnosis. This is particularly true in cases where pump installations are in dangerous or remote environments, such as on offshore platforms or in water treatment facilities. Operators can remotely access digital twins to monitor system data, simulate performance scenarios, and conduct diagnostics. This method significantly cuts costs and time associated with inspections by going off-site instead.
Overall, digital twins in contemporary pumping systems provide numerous advantages that benefit businesses improved predictive maintenance, sophisticated design and optimisation processes, better operational efficiency, and remote monitoring capabilities are just a few examples of their many benefits. As technology progresses further, their use will likely grow ever more important – helping companies realise innovation, reliability, efficiency, and recognition of pumps as essential assets while creating sustainable performance through virtual asset models. In essence, digital twins are transforming pumping systems from simple machines into intelligent, data-driven assets that drive significant value for industries, including industrial intelligence of things (IIoT) and decarbonising pumping stations.
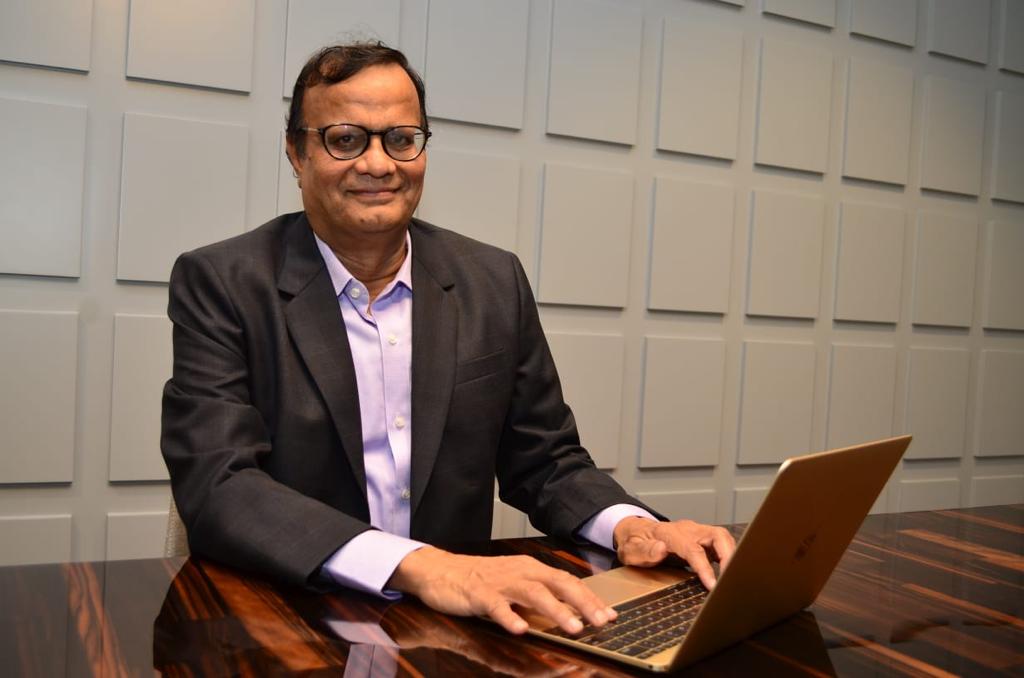
Anil Sethi, Founder & Chairman, Pump Academy Private Limited (iPUMPNET)