Successful robotics connectivity only happens by design. Intricate and delicate electronic systems must work to monitor, control, and adjust robotic performance through real-time adjustments. When it is well designed, the result is a reliable high-performance network of machine systems working to keep industry moving. This blog explores some of the critical design aspects that engineers should consider when designing for either industrial or commercial robotic applications. By taking into account the generally rigorous and harsh demands of industrial robotic systems, one soon realizes that in many applications that require reliable solutions under the most extreme conditions, specially designed industrial products from TE Connectivity (TE), a leader in harsh environment connectivity and sensing applications, are best suited for the task (Figure 1).
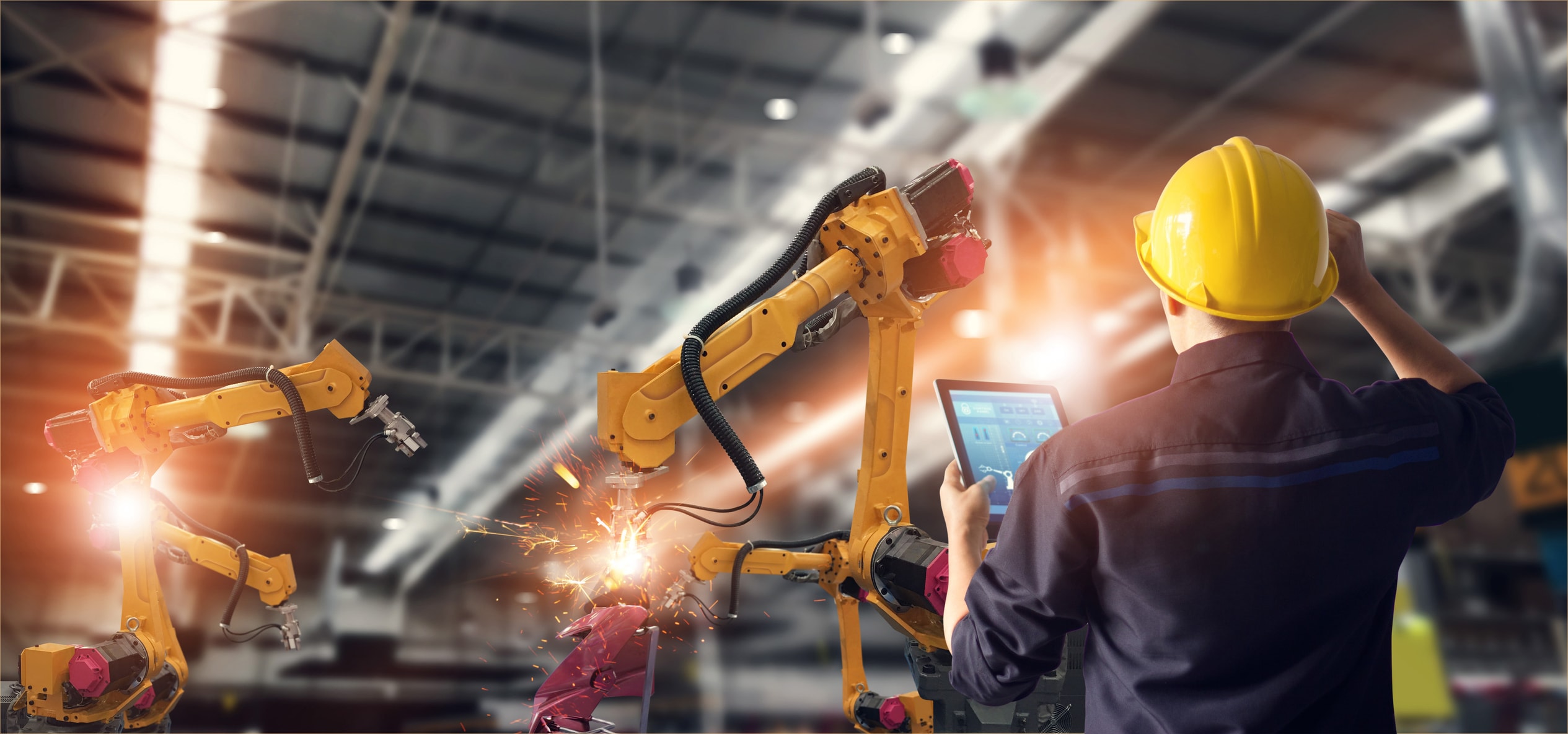
Lasting Endurance
TE endeavors to provide products that are compact, rugged, and reliable. Rugged solutions call for robust technological architectures, which require their components get designed for durability, resilience, and longevity. To this end, TE designs with these factors in mind. By analyzing what types of environmental stresses these components must withstand, and factoring in the time duration of these stresses with equipment life cycles yield, one obtains an expectation of the high-performance requirements needed. TE generates test criteria to help ensure that any production items will survive and perform in the field to meet stringent expectations. With TE’s portfolio of connectors, sensors, and more, designers can put more data, power, and signal into their industrial robotic systems.
Protection & Durability
Protection and durability are built-in by design. As a leading provider of connectivity products, TE has the technologies, operations, and a long-standing reputation that ensures designers can trust their robotics connectivity to them. TE understands the industry’s need for reliable connectivity that delivers greater simplicity, efficiency, and uptime. This is why TE’s communications and networking solutions are geared to the most demanding requirements of manufacturers worldwide as they approach the Internet of Things (IoT). Networked manufacturing enables seamless communication as well as higher speed and efficiency. TE manufactures industrial sensors with the packaging to support harsh environments, low-current consumption, and a variety of measurement types to enable the growth of Industry 4.0. In addition to data transfer on the factory floor, TE designs its products to share information throughout the entire production environment—beyond the industrial setting and onto desktops. TE works with engineers to push the boundaries of efficiency and productivity—enabling simpler, faster, and more economic industrial communications.
Rugged Environments
Industrial products are built to withstand rugged environments, including moisture and contaminates. By addressing designs to fulfill Ingress Protection (IP) and National Electrical Manufacturers Association (NEMA) codes, TE delivers products that prevent the ingress of water and foreign objects (e.g., dust or fibers), as well as corrosive agents and various gases and atmospheres.
Exceptional cold wreaks havoc on parts, causing them to be brittle and stiff. Failure rates increase as the potential for physical damage, through cracking or other introductions of physical defects, rise. TE Connectivity’s Intercontec Connectors can sustain operation in temperatures down to -20°C and up to 130°C (Figure 2). They also provide IP66/67 protection when connected. Overall, these connectors are designed for use in a wide variety of applications, including robotics, drive systems, mechanical engineering, automation mechatronics, medical/chemical engineering, packaging and printing, and aerospace.
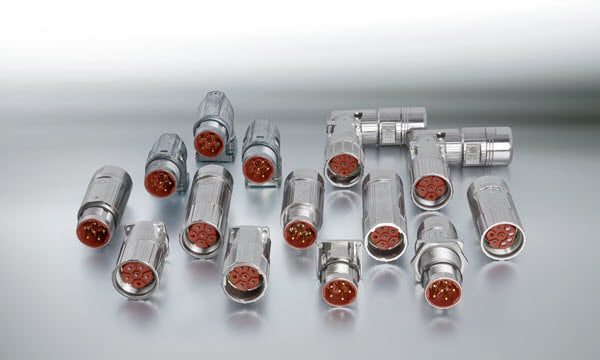
Industrial and robotic equipment are often subjected to some of the most extreme forms of vibration. Relative movement stemming from an aggressive and highly dynamic motion profile may push connector systems to their limits. TE offers products designed to specifically minimize relative movements and ensure long-lasting and reliably stable connections. Parts and systems are designed to withstand high g-forces in various axes to endure the ongoing and continuous physical jarring and shaking, rendering them tenacious and essentially indefatigable. TE Connectivity’s Dynamic Series Ruggedized Connectors meet the rigorous demands emanating from high-vibration applications (Figure 3).
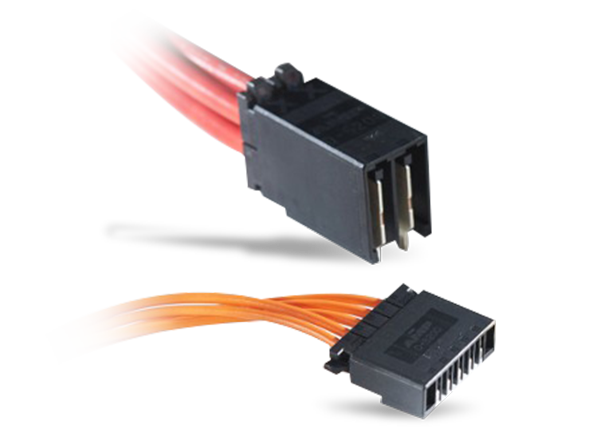
Reliable Connections Made Easy
Polarized connectors or mechanically keyed connectors significantly aid in the connector mating process by helping to prevent mismating, guaranteeing positive alignment and proper connection primarily when the connector is located in hard to reach places or in instances when a blind connection might be required. Polarized connectors help eliminate unwanted connections from occurring. In an associated manner, modular connectors provide flexible and quick adaption to the requirements of the application.
High-cycle count connectors mean they can engage and disengage often without degradation. Therefore, high-cycle count connectors indicate that the connector design is durable because no electrical or mechanical defects are expected to occur as a result of repeated distinct connecting.
TE’s temperature sensors, along with their high-voltage contactors, provide the ability for high-performance industrial operation. TE’s separable connectors transmit power to equipment where it is needed. TE provides hook-up wiring and multicore cables that deliver the power and signals required to communicate in today’s connected world.
Conclusion
Industrial products from TE are specially designed for endurance, protection, durability, environmental rigor, wide operating temperatures, vibration immunity, high-cycle count connectivity, and easy mating. TE Connectivity industrial solutions work to ensure successful robotics connectivity design for every high-performance industrial application. Delivering more data, power, and signal into industrial robotic systems produce more exceptional results that will have robots and their human overlords smiling.

Paul Golata joined Mouser Electronics in 2011. As a Senior Technology Specialist, Paul contributes to Mouser’s success through driving strategic leadership, tactical execution, and the overall product-line and marketing directions for advanced technology related products. He provides design engineers with the latest information and trends in electrical engineering by delivering unique and valuable technical content that facilitates and enhances Mouser Electronics as the preferred distributor of choice.
Before joining Mouser Electronics, Paul served in various manufacturing, marketing, and sales related roles for Hughes Aircraft Company, Melles Griot, Piper Jaffray, Balzers Optics, JDSU, and Arrow Electronics. He holds a BSEET from the DeVry Institute of Technology (Chicago, IL); an MBA from Pepperdine University (Malibu, CA); an MDiv w/BL from Southwestern Baptist Theological Seminary (Fort Worth, TX); and a PhD from Southwestern Baptist Theological Seminary (Fort Worth, TX).