The success of electric vehicles in the construction industry will largely be determined by battery prices being low enough that the total cost of ownership is cheaper than diesel alternatives. IDTechEx’s new report, “Electric Vehicles in Construction 2023-2043”, shows that there is a battery price tipping point, under which it will be cheaper over the vehicle lifetime to operate an EV. Selecting the right chemistry then will be imperative for getting a low enough vehicle price. So why is a clear dichotomy seen between the batteries being deployed in China compared to Europe?
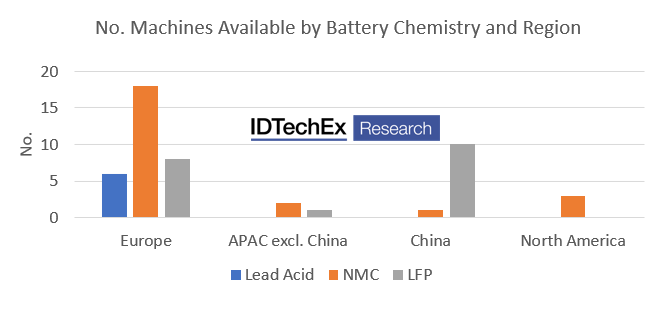
Electric vehicles in construction are an emerging market. Despite this, IDTechEx has built a database of more than 100 example makes and models across seven different construction vehicle categories. However, with lots of vehicles still yet to be released, only 49 database entries have confirmed chemistry information. With Europe and China being more established markets for electric construction vehicles, conclusions about battery chemistry trends from OEMs in these regions can be made. What is obvious at this early stage is that Europe heavily favors NMC, while China has chosen LFP.
Battery Requirements in Construction Vehicles
So why would one select NMC, LFP, or even lead acid, for that matter? Electrifying construction equipment is a fascinating and nuanced topic. The priorities for a battery are huge capacities at low costs. With some of these machines being gargantuan, and usually requiring concrete counterbalances to handle the massive loads they encounter, battery weight isn’t so much of an issue. Power density is also not much of a priority. Unlike electric cars, construction vehicles do not tend to have large spikes in power demand and are more likely to operate at a steady rate for a long time. As an example, the Tesla Model S has a ~60kWh battery and ~210kW motor power, meaning its battery must be able to deliver a peak of 3.5C (power divided by capacity). This is a typical requirement of road cars; hence, they tend to favor power-dense chemistries like NMC. By contrast, the Volvo L25 electric (an electric compact loader) has a battery capacity of 40kWh and a maximum motor power of 36kW, so the battery is only required to discharge at a maximum of 0.9C, well below road car expectations.
The same is true when you move to the really big stuff. The XCMG XE270E is a 27-tonne excavator leviathan with a battery capacity of 525kWh, but its motor is a measly 140kW (~0.27C). In fact, research in IDTechEx’s report, “Electric Vehicles in Construction 2023-2043”, shows that the vast majority of electric construction vehicles have a peak discharge requirement of less than 1C, with one quarter of vehicles requiring less than 0.25C peak discharge.
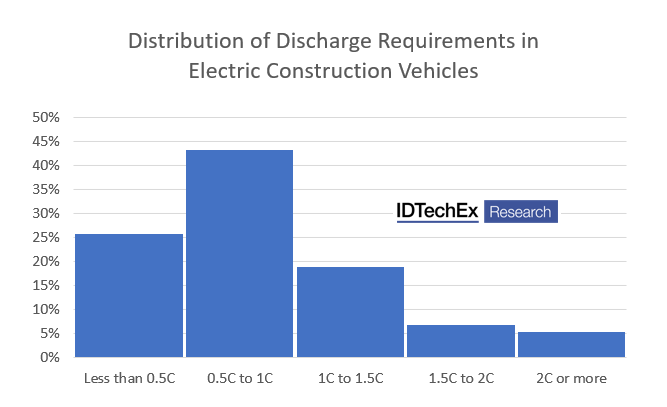
A low peak discharge requirement can be fulfilled by lead acid batteries, which is likely why it had a brief moment in the sun in the early days of construction electrification. The European examples that used lead acid were mainly from the mid-2010s, at which point lithium-ion technologies were still scaling and were much more expensive than lead acid. However, these vehicles were seriously limited, with low endurance and slow recharge times, making their use a challenge. Lead acid was quickly replaced with lithium-ion as it became more financially viable.
Both NMC and LFP offer the required performance for construction, happily coping with the peak discharging requirements and having high enough volumetric and gravimetric densities to fit in the machines. Speaking broadly, NMC tends to be a higher-performance battery than LFP, with better energy and power densities but coming at a premium. It would make sense then for the industry to select LFP. It offers all the needed performance while helping minimize the premium of building an electric vehicle, the number one priority for electric construction vehicles. Why, then, does the European market mostly use NMC?
Why is NMC dominant in Europe and LFP in China?
The best explanation is that it has been a case of availability. Most of the electric construction development so far has used battery pack suppliers, such as Northvolt, Forsee and Volta, and most of their products use NMC. IDTechEx’s research finds that over 75% of the offerings from European and North American pack manufacturers use NMC. These companies have been supplying a range of industries, including heavy-duty road vehicles like buses and trucks. These vehicles will have quite high peak power to deal with acceleration events, hills, etc. and will likely suit NMC better. IDTechEx speculates that this is why Europe has been mostly choosing NMC so far, but with battery pricing being a key factor in the success of electric construction vehicles, it is likely that there will be increased LFP uptake in the future.
Meanwhile, in China, LFP is already the dominant chemistry choice. China already has a good supply of LFP solution. This has risen as its vehicle fleet has rapidly been electrified, and it needed a cheap solution that could provide acceptable energy density (vehicle range) and keep the vehicle affordable. By contrast, European and North American electric vehicle markets have focussed on maximizing vehicle range, normally opting for the more expensive NMC and anticipating consumers will be more comfortable with the additional cost. This is good news for China’s electric construction industry, which has been able to build very large batteries relatively quickly and deploy some huge machines, such as the XCMG example already mentioned.
Unfortunately, there is not much data concerning which North American or APAC-based OEMs favor battery chemistries. This is mostly because OEMs in this region are only just beginning their electrification journeys. North America is a prime example; giants of the industry CAT and John Deere have made a recent push with electric construction vehicles showcased at BAUMA 2022, CES 2023, and CONEXPO 2023. However, these are still some years away from production, and battery chemistries are yet to be confirmed. However, an educated guess would suggest that CAT will likely use NMC for similar reasons to Europe.
Sodium ion, a Future Candidate?
Another possible contender for the construction industry is sodium-ion. This is an emerging chemistry and does not have an established market yet. The key thing to know is that sodium-based solutions can be produced at lower costs than lithium ones, but they will not have the same performance. In this respect, they share the qualities of LFP. The issue is that they are not yet a scaled solution, so they are more expensive than both LFP and NMC while having worse performance. Sodium, therefore, does not make sense in the construction industry for the time being. However, when scaled and delivering the promised price reduction, it could be a prime match for the needs of this nuanced market.
The electric construction industry is still nascent, with few vehicles in series production. However, if recent activity and announcements are to be believed, then the number of machines available in the next few years is going to explode. In IDTechEx’s report, “Electric Vehicles in Construction 2023-2043”, a 10-year CAGR of 37% is forecasted, with the electric construction machine industry growing to a value of US$150 billion in 2043. All of this growth is going to give rise to a significant battery demand, and whether it be NMC, LFP, or perhaps even Na-ion, the evolution of this industry is going to be electrifying.